- February 2, 2017
- 3 Comments
The Basics: Welding for Beginners
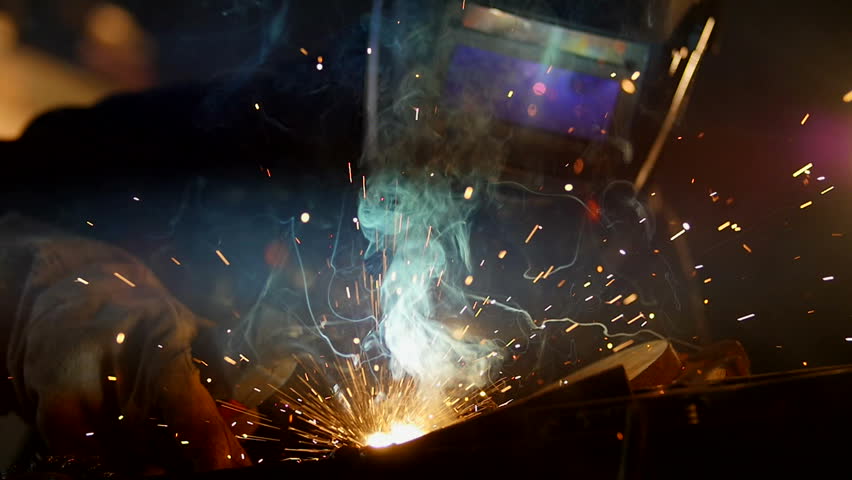
Welders are everywhere, and they are doing amazing things. From diving a few hundred feet underwater to repair a few holes sprung in a steel ship out at sea to out in the cold vacuum of space, welding on a spacecraft that requires repair…Or even (and just as practical) you might just find an old bloke that simply wants to weld together a nice new steel table for his workshop.
Whatever the case, if you’re interested in taking up welding yourself, enrolling in specialised training to suit your goals is always the best way to learn. If you’re a DIY type of person and enjoy a little trial and error, this article can serve to help you understand some of the basic process and rules when it comes to beginner welding techniques.
Safety
First off, like with any work in the machine or steel working industry, a conversation on safety is necessary. For beginners, understanding the dangers and safety precautions necessary in the workplace is a fundamental step in becoming a great welder.
For the sake of avoiding this article becoming a guide on workplace safety itself, we highly recommend reading Safe Work Australia’s Model Code of Practice on Welding Processes. This outlines everything you need to know about safety standards, discussing all topics from identifying possible hazards to proper ventilation and protective equipment.
Understanding the Process
Basic welding is more than just melting two pieces of metal together, first you must consider the type of welding machine you will use and what job you’ll be using it for. The most basic form of welding, and a great start for beginners, is Arc welding.
Now there are a variety of different methods of Arc welding, although the most common processes are Metal Inert Gas (MIG) welding, Tungsten Insert Gas (TIG) welding and Stick welding.
MIG Welding
MIG Welding is regarded as the easiest type of welding to learn, it works by using a wired welding electrode on a spool that is automatically fed through at a constant speed as you work. The arc melts the wire and joins it together at the base, resulting in a strong and clean weld.
The reason why gas is used in this welding technique, is because it provides a shield of fog that surrounds the puddle of hot liquid metal created when welding at intense temperatures. This gas shield keeps the weld puddle free of any contaminants and is what helps ensure a strong weld with low porosity (the empty spaces in a material). This process is useful in welding a variety of materials such as mild steel, stainless steel and aluminum.
A clear downfall of this method though, is using a gas requires an environment usually indoors and away from any wind or elements that might blow the gas away. This can be remedied with gas-less MIG welding, which uses flux-core wire. Flux-core wire is similarly fed through automatically and is made with a coating that creates the gas while you weld- This option provides a messier finish, with welds requiring more clean-up, and flux-core wire can be pricey.
TIG WELDING
TIG welding, on the other hand, is harder to learn and takes some practice before you can master it.
TIG welding is more physically complicated, as it requires a large welding rod to be fed manually into the weld puddle, and also uses a protective gas to protect the weld puddle. When TIG welding, you need to simultaneously: control the torch, feed the wire, move at correct speed and also use the correct current. This is usually used for thinner gauged metals and can be applied when working on toolboxes or kitchen sinks for example.
STICK WELDING
Similar to TIG, Stick welding involves using a fixed length electrode in joining metals, being a fixed length, the electrode is manually fed by the welder. Most DIY welders go to Stick welding as a basis for learning how to weld.
This welding technique is one of the most versatile, inexpensive and forgiving processes of the craft. It can be done in just about any setting and is a good choice if a basic joint or attachment is required.
A downside to stick welding though, is that it often provides a messy finish and would not be a viable option where a smooth, clean finish is desired (such as in sheet metal working for automobiles).
Miller Electric, offer a great read on improving Stick welding technique through their CLAMS guide, which provides all the informative and necessary steps to consider when beginning stick welding.
These points being:
- Current setting
- Length of arc
- Angle of electrode
- Manipulation of the electrode
- Speed of travel
What is more, an understanding of the settings for Stick, MIG and TIG welding can help you in grasping the concepts behind various other techniques of welding.
Tips for Best Practice
Now that you have a better understanding of some basic welding techniques and the process behind them, here’s some quick tips we at Machines4U would recommend to any beginner welder:
- Understanding AC and DC currents. Learning what current to use for your job is a necessary step in getting a strong weld. Depending on the job and the tools you use this can vary.
- Clean the material before starting. A good scrub with a wire brush, grinder or sandpaper will remove a majority of the dirt and rust from the material, this helps to get a stronger weld and better porosity.
- Remember to put your helmet down. Even some of the most experienced welders are known to forget this step, most of the time because their hands are preoccupied or they simply forget in the process of things. Remember that you can’t weld without working eyes!
- Tacking is a necessary step as it ensures the material is secure and in place before welding. Tack welding is putting short, set-up welds that hold the edges together and are easily correctable if a part needs to be dissembled and re-secured before welding.
- Have your head to the side, away from the smoke, is also best practice so you have full view the joint as you weld.
- Some basic and useful welds that are great for beginners to practice are:
- Butt joints
- Lap Joints
- T Joints
- Spot Welds
- A grinder will soon become your best friend. It’s safe to say if you’re new to welding your first one, two or 30 attempts to at welding something specific won’t turn out as planned. But never fear! a grinder can cut that bad boy back like nothing ever happened. Patience helps too.
- Blueprints. If not taking a specialised course, taking the time to understand blueprints can go a long way in helping you understand the reason and uses for welds in practical applications.
- Popcorn or Bacon? Many might tell you if your welding sounds like popcorn popping in a microwave your settings are either too hot or too weak for the job. Teachers often say to listen for that sweet sound, similar to bacon frying in a pan, to know if your weld is at a good setting.

This article only scratches the surface on the craft and if you will leave with only one piece of information before starting, let it be that safety is always first!
In the market for welding supplies? For everything from helmets to purge monitors visit here.
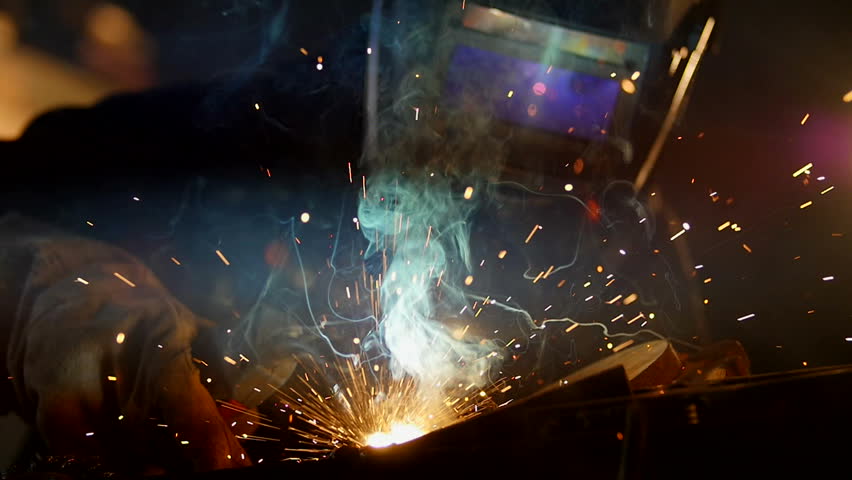
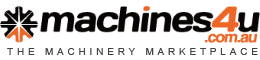