- February 7, 2017
- No Comment
The Complete Guide To Metalworking Tools
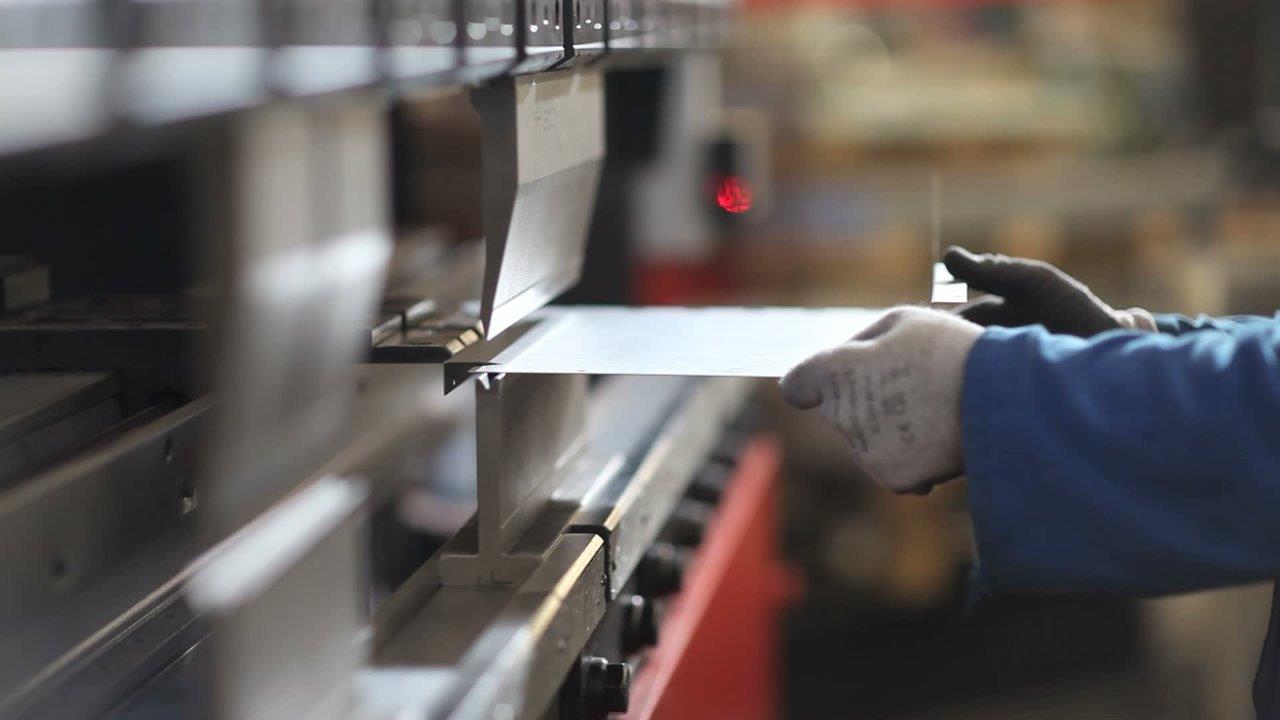
In this guide we take a look at the machines and metalwork tools that can make shaping even the hardest of metals look like running a hot knife through butter.
Hand Metalworking Tools
In any workshop, hand tools are the foot soldiers that help a craftsman reach their final product. They may only have simple applications, like measuring and marking, but their use mean the difference between a rookie and a master craftsman.
Here is a short list of some metalworking hand tools you’d see in most workshops.
Scriber & Scriber Block
Use: The scriber is a marking tool, used for marking lines on parts. They produce thin, semi-permanent scratch marks on the surface.
Tips:
- Scribers advantage over pencil marking is that they don’t erase easily, are more accurate and easier to see on metal.
- A scriber block is used to layout lines at a set height. This works by holding the piece against an angle plate and adjusting to the required height.
Calipers
Use: Calipers come in various forms and are used also as a measurement tool. The outside caliper is one of the most commonly used in metalworking, measuring large distances and diameters.
Tips:
- Calipers provide high accuracy, repeatable measurement
- Each form of caliper is used for various situations. For example, outside calipers are used generally for measuring pipe.
Card Wire Brush
Use: A simple cleaning tool, the card wire brush is used in metalwork for cleaning when pinning occurs. The teeth of the file remove any particles or pins clogged in files.
The Centre Punch
Use: The centre punch tool is used in metalwork to mark the centre point of a hole before drilling. It involves hammering the tool, producing a dimple (mark) on the metal.
Tips:
- The centre punch should act as a guide for the drill.
- An automatic version of the tool is available.
Soldering Iron
Use: Large soldering irons are used for soldering joints in sheet metal objects. They are also used in soldering copper plumbing, joining heavy wires and keeping metal surfaces hot.
Tips:
- The metal surfaces must be clean and shiny. Cleaning ensures the metal won’t form another coating of oxide.
- Check the joints to be soldered must be mechanically strong before the solder is applied. Don’t depend on the solder to hold the pieces together. The solder serves as more of a filler rather than a bonding agent.
- The iron tip should be coated with a thin film of solder.
- When soldering, the torch should be used to heat the pieces that form the joint until the metal is hot enough to melt the solder on contact. The heated metal then melts the solder as it is fed into the joint
Panel Hack Saw
Use: Used for soft and sheet metals, panel hack saws are made from a frame of wrought iron and are used when cutting thin sheets of metal.
Tips:
- Select the correct blade for each material
- It’s best to mark the cut before cutting and secure the piece in a vice grip
- The metal should not flex or bend when cutting
- Filing is required after cutting metal, so to remove any sharp edges
Sheet Metal Forming Tools
Primarily utilised for sheet metal forming and manufacturing, this section lists some handy machines that help bend, curve and cut metals. Here are a few metalworking tools that bend steel like rubber.
The English Wheel
Use: The English wheel is used to shape metals into compound curves and is used in the automotive and aircraft industry. Mainly used for steel and aluminum, the English wheel works by pushing material back and forth between an upper and lower wheel.
Tips:
- There are six different angle wheels, each altering the shape the metal will form
- More pressure will be applied to the sheet metal if the gap between the wheels is smaller
Power & Planishing Hammers
Use: Depending on the power required, power and planishing hammers shape sheet metals. Planishing hammers are powered by an air motor and the die impacts both surfaces of the metal and strengthening it. Power hammers on the other hand are electric and use a fixed stoke to perform metal shaping tasks.
Tips:
- Various forming methods can be carried out with this metalworking tool, such as doming, beading, edge turning and shrinking
Shrinkers & Stretchers
Use: This metal shaping tool involves the operator stepping on a pedal which forms the metal to to their desire. Common applications are in metal shaping for light framing or body work in the automotive industry.
Tips:
- Drawing a blueprint on the metal piece is can help achieve the desire shape
- Consistency and understanding the pressure applied to the metal is key to good shrinking and stretching.
Benders
Use: Used in shaping pipes and bars, there are a variety of benders that work both manually and electrically in bending metal tubing.
Tips:
- If looking for cost-effective, fast and easy bending, a pipe bender is the better option
- Spring benders are cheap although they are more difficult to create a bend with
Press Brakes
Use: Press brakes are one of the most satisfying machines to watch operate. This metal shaping tool works by bending sheet and plate metal, clamping the piece between a punch and die.
Welding Machines
Use: One of the oldest and most versatile metalworking tools, welding has been used since the bronze age to join, braze and cut metals of all shapes and sizes.
Mastering the craft of welding often takes years of practice and some degree of formal education. That being said, for most simple jobs welding is a useful DIY craft to learn.
Tips:
- Take the time to understand all the safety guidelines and regulations before beginning welding
- For most jobs stick welding is a cheap and effective process
- Take the time to learn other basic welding techniques such as TIG, MIG and Arc. Each have their own strenths and weaknesses
Machining Metalworking Tools
In this section we list some of the most common industrial machines used for manufacturing purposes. These metal machining tools are accurate, produce clean finishes and can be difficult to use without the proper training.
Milling Machine
Use: Milling machines work to remove unwanted material from a work piece, done through the use of rotary cutters. It can be used anywhere from small individual parts to large, heavy-duty ones.
Tips:
- Get an indicator with a vertical dial. This beats craning your neck when zeroing a part
- Special-toothed wedges are effective as backstops in a mill
- Buy two drill chucks with different diameter shanks on them. This allows you to save time on tool changes when you have the same shank diameter as your cutting tools
- Don’t put an end-mill in a quick-change drill chuck. This is tempting at times but is a pure rookie move. If the end-mill chatters for a billionth of a second, the chuck loosens and all hell breaks loose!
- Remove the draw-bar every so often and put a drop of oil or light assembly lube on the threads. You should be able to spin this with your pinkie. If it doesn’t spin freely, get a new one
Bench Grinders
Use: Bench grinders are fixed atop a bench and featuring driving abrasive wheels. Depending on the grade of the grinding wheel, bench grinders can be used to sharpen tools to roughly shape metals
Tips: Taken from Canadian Center for Occupational Health and Safety
- Fasten pedestal and bench grinders on a solid surface securely
- Ensure all the guards are in place and secure before using a grinder
- Adjust tool rests to within 3 mm (1/8 in.) of wheels. Never adjust rests while wheels are moving. Work rest height should be on horizontal centre line of the machine spindle
- Maintain 6 mm (1/4 in.) wheel exposure with a tongue guard or a movable guard
- Check that wheels have blotters on each side
Metalworking Lathe
Use: The lathe is one of the most used pieces of machinery in most workshops. It’s used for shaping metals, wood and plastic and come in various forms.
Most lathes work simply by rotating and cutting a work piece into a desired shape. One form of the lathe, the turret lathe, is a specialised version that is usually used in mass production jobs for specialised parts, such as steel chess pieces.
If you’re just starting out using a lathe, this website offers a user-friendly guide on beginner lathe operation.
Visit: www.steves-workshop.co.uk/tips/lathetech/lathetechindex.htm
Buffing Wheels
Use: Often the last step for processed metals (and the last machine for our list), buffing wheels are used in metal working to polish the surface of metals, providing a mirror-like finish.
This process is used to enhance the appearance of a material, prevent contamination, prevent corrosion in pipes and remove oxidation.
Interestingly enough too, you can also polish metals with a bench grinder if you have the right replacement parts.
Think we should have mentioned other metalworking tools? Leave a comment below!
Visit the Machines4U Marketplace for a comprehensive list of parts and machines.
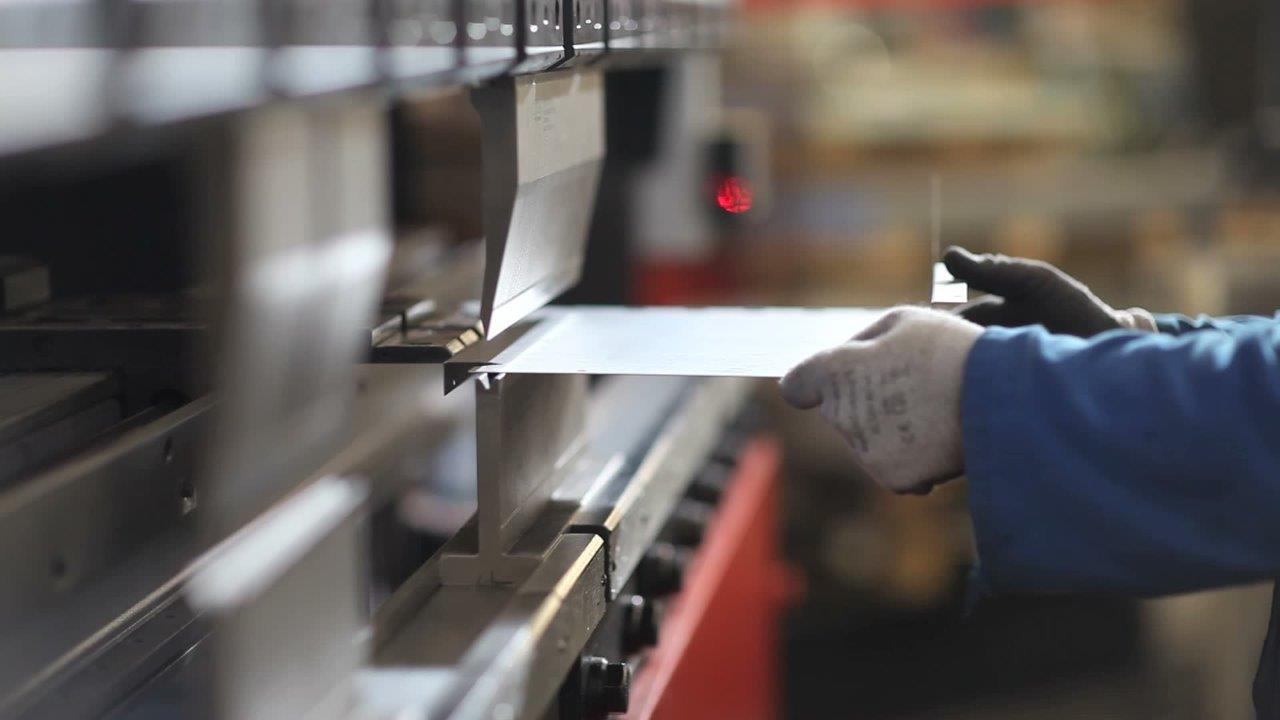
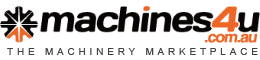