- February 2, 2017
- 2 Comments
6 Types of Welding You’ll Want to Know
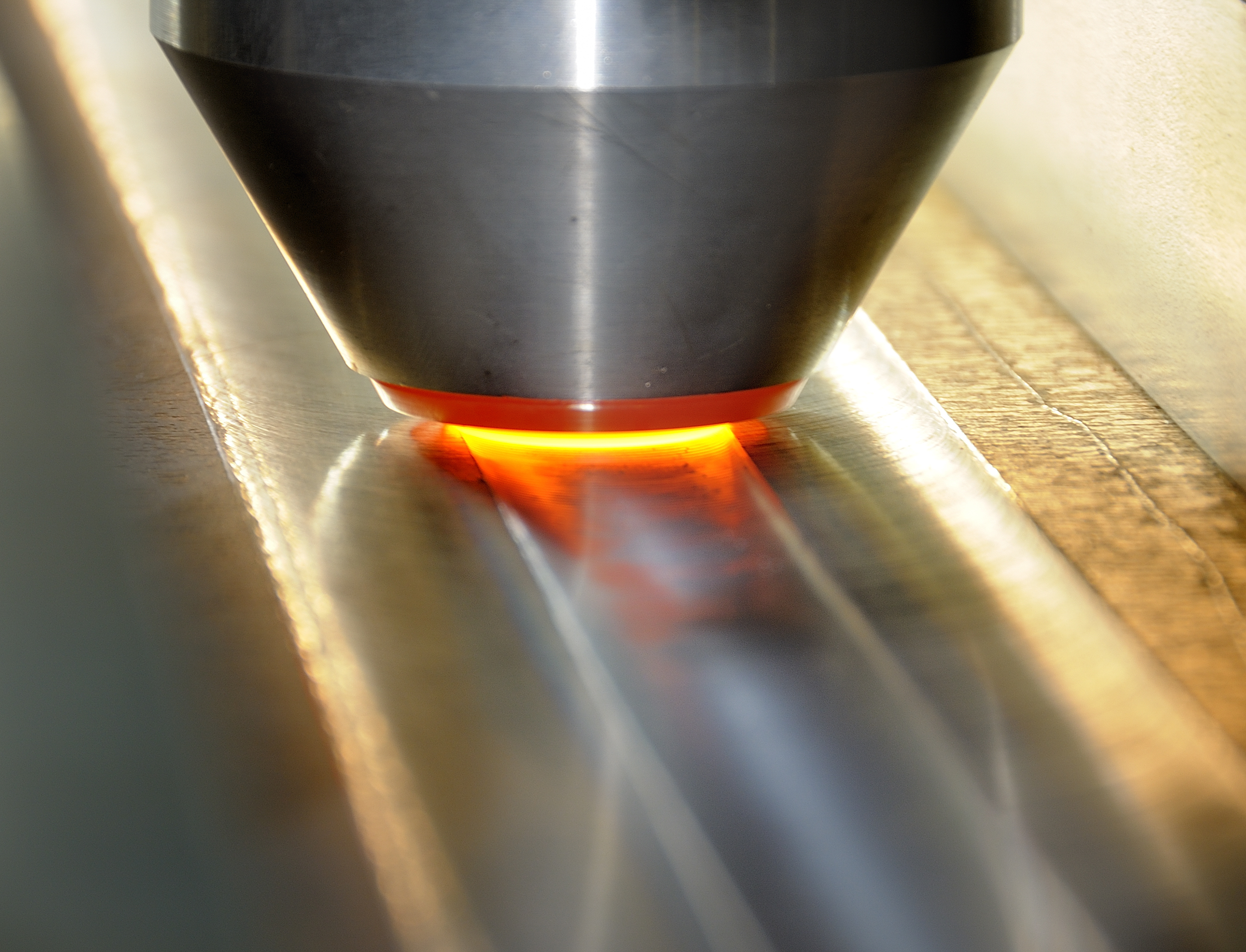
If you’ve already learnt about the basic forms of Arc welding (MIG, TIG and Stick) from our Welding Basics article, you’re probably curious about the various other types of welding. In this article, we talk about some of the most advanced and interesting welding techniques used in the world today.
Cold Welding

Cold Welding is arguably one of the most phenomenal forms of welding known to man. Also referred to as Contact welding, this form of welding occurs when joining takes place without fusion or heating.
There is no liquid involved and the material does not experience a molten phase.
You’re probably wondering, how is this even possible?
Cold welding works by causing the metallic bonds (the agent that holds the atoms together in materials) to link the gap between metals and essentially fusing them into a single object. For example, if two, bare, steel rods were touching in the vacuum of space, they would soon become inseparable.
This happens because there is no oxygen in space, thus, the metals do not experience oxidation on their outer layers. This oxidation is a key element in what prevents metals from sticking to each-other, here on earth.
American Theoretical Physicist, Richard Feynman, commented this phenomena, in 1963, stating: “The reason for this unexpected behavior is that… there is no way for the atoms to “know” that they are in different pieces of copper. When there are other atoms, in the oxides and more complicated thin surface layers of contaminants in between, the atoms “know” when they are not on the same part”.
Ref: Richard Feynman, The Feynman Lectures, 12–2 Friction
Hyperbaric Welding

Moving 330,000 ft back down to sea level, Hyperbaric welding or Underwater Welding, is prominent in the manufacturing industry for structural applications. Hyperbaric welding allows welding teams to fix any issues with ships out at sea, saving the time and costs involved with dry docking. This can be done both dry and wet settings.
Dy welding works at a raised pressure, and involves the weld to be performed within a chamber filled with a mixture of gases, sealed around the structure needing repair.
Wet welding on the other hand directly exposes both diver and electrode to water. Because of this, the electrode required for welds is made with a waterproof coating, the welding power supply is connected via cables and hoses and the process is generally restricted to steels with low-carbon to avoid the risk of hydrogen caused cracking.
Ultrasonic Welding
As you might have taken from the name, the method involved with Ultrasonic welding machine exposes ultrasonic frequencies to the metal, causing them to fuse.
Operating at frequencies above kHz, The shear stress experienced by the metals results in the decomposition of the surface oxidation, thus, fusing the two surfaces fuse together.
This is also the fastest method of welding, taking less than a second to set, and is highly present in electrical, automotive and packaging industries where a precise and, solid weld is needed quickly, generally with thin metals.
Friction Welding
Another machine that uses speed and sheer force, through a process that essentially rubs the two metals together, is the Friction Welder.
Friction welders work through the rotation of one work pieces at an insanely high Rpm and the other held in a fixed jaw. A lateral force is then induce a to connect the objects and as a result, the intense heat generated from the mechanical friction, leaves no choice but for the metals to forge together.
This method of welding is beneficial for manufacturing industries as they take seconds to join and do not involve any melting- this removes the chance of grain growth in engineered materials.
Orbital Welding
Achieving a perfect circular weld has never been easier, with Orbital welding machines specialising in mechanically rotating the welding arc 360° around a work-piece.
Commonly used to weld pipes and tubes, their consistency, precision and work speed, has also found benefit in crafting material for the Aerospace and Pharmaceutical.
Orbital Welders have the ability to work in the smallest of situations, with tubes of up-to 1.6mm small, and works at a weld-rate of about 5 inches per minute, depending on the metal thickness.
Seam Welding
As satisfying as watching a hot knife slice through butter, Seam welding is used in the industry to produce a weld at the faying surface of two metals of similar or the same material.
A Seam weld uses two disc-shaped electrodes that rotate continuously, as the work-piece passes between, welding them together. This welding technique is generally used for making items like boilers, drums and tubing,
The welds produced by Seam welds are extremely durable, as the joint is not only welded together but also forged. For this reason, in competitive racing circles, Seam welds are also utilised for their exceptional rigidity in chassis and strut towers.
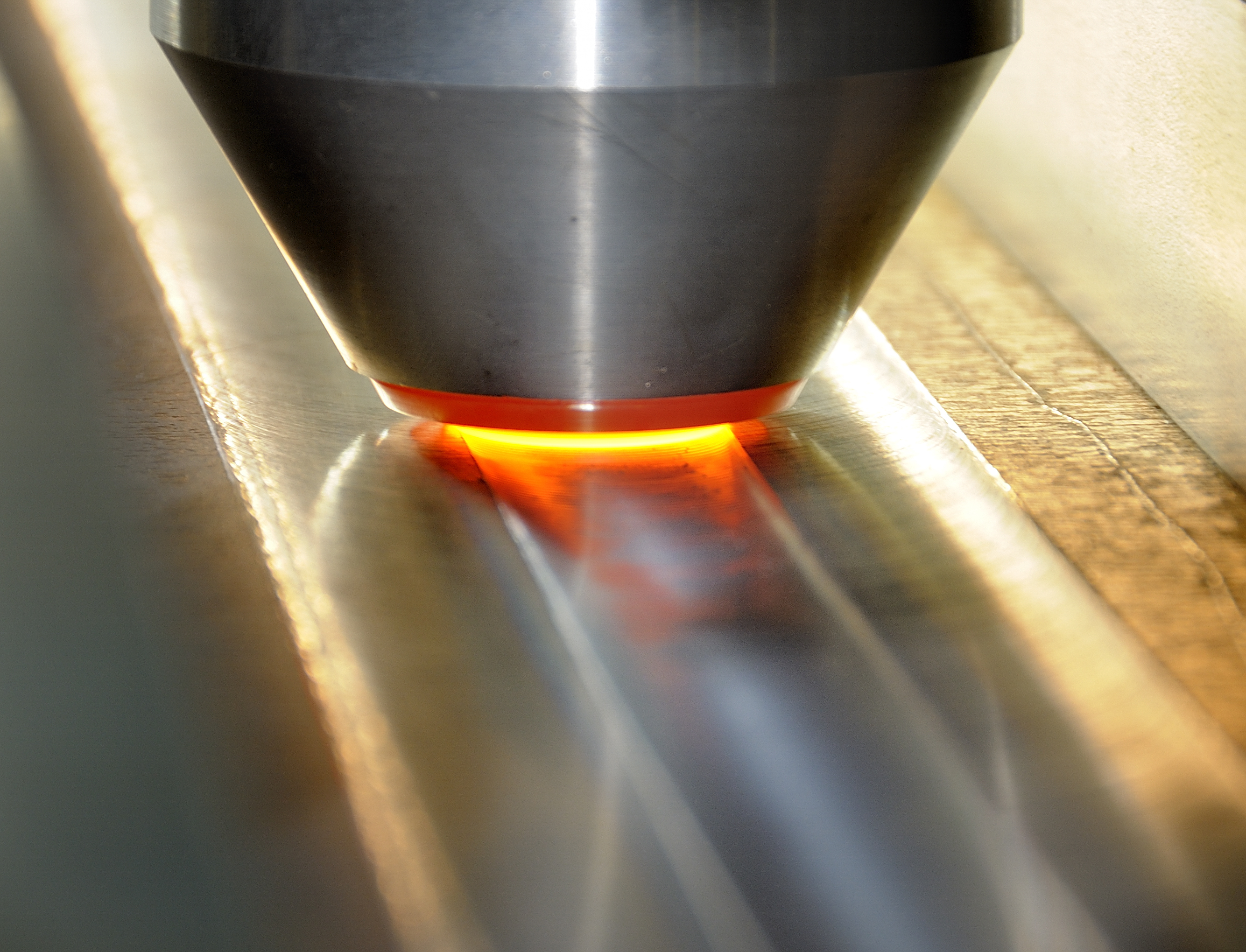
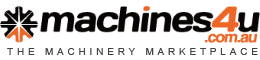