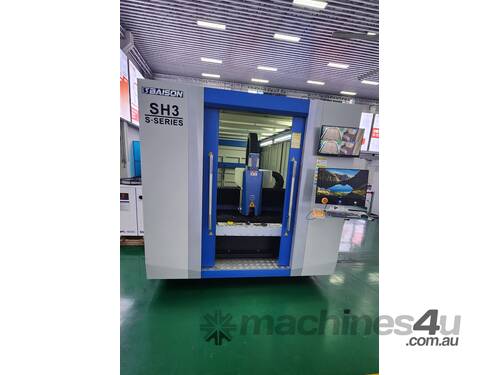
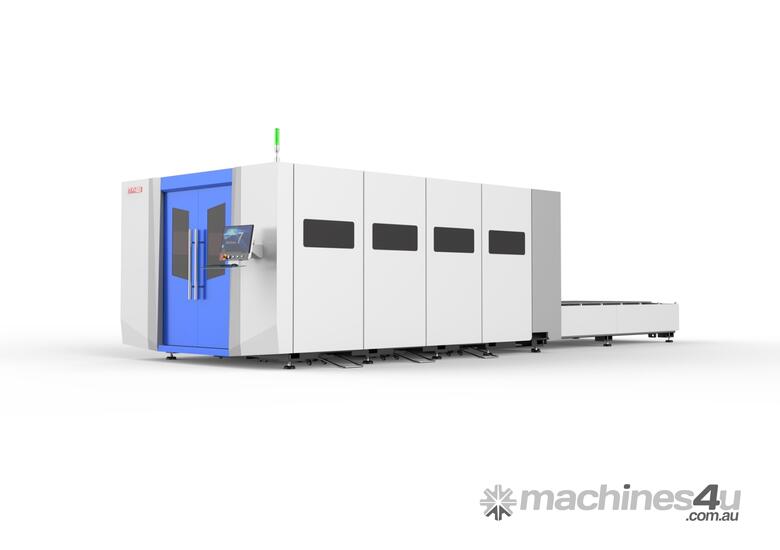
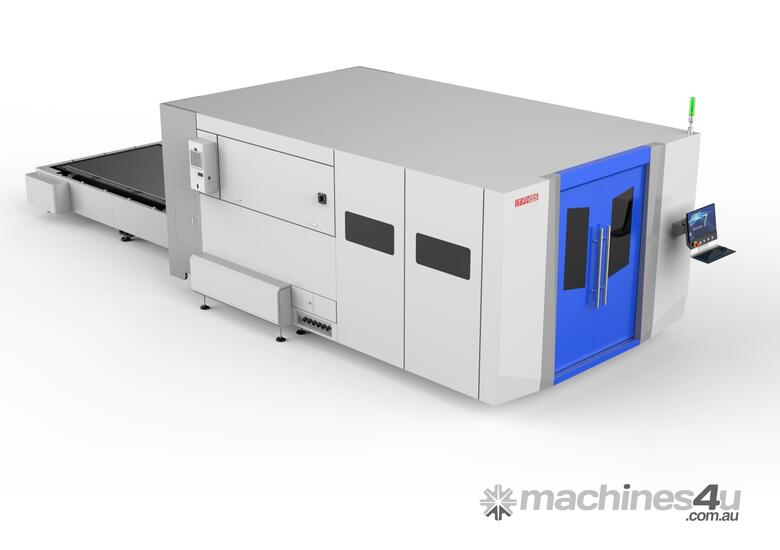
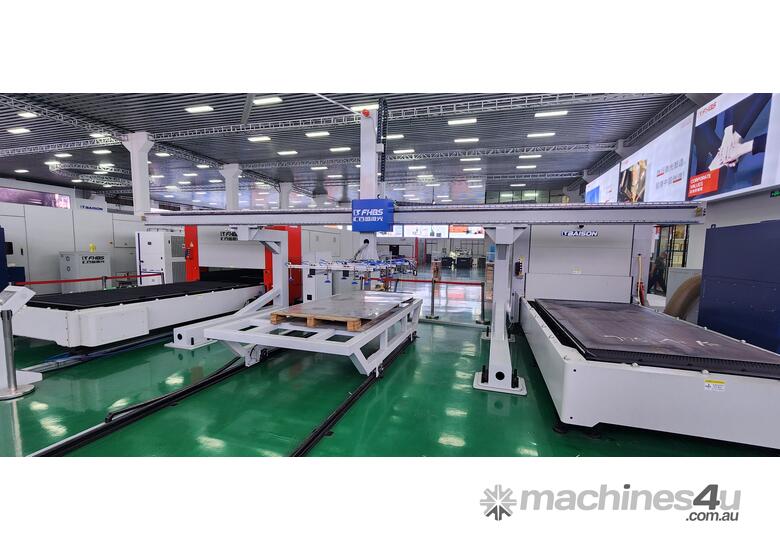
ALFRA - COMPACT 32mm Capacity German Made Quality German made. Say no more. One of the most powerfull onsite tools you will use. Features Quality German made drilling machines. perfect for all onsite work powerful motors....
CNC MACHINERY SALES AUSTRALIA PRESENTS - New Litz Hitech LH-630 Twin Pallet Horizontal Machining Centres. Features Pallet Sizes 630mm x 630mm Travels X Y Z 1000mm x 850mm x 950mm Up to 10,000rpm BT50 or 12,000rpm BT40 Fa....
Energy-independent solution for the horizontal handling of non-porous sheet and plate material. It has a telescopic front handle bar and adjustable vacuum pads. The battery-operated warning device ensures a high degree o....
We are a waterjet cutting system manufacturer with 20 years experiences. So we provide reliable waterjet cutting systems with factory price. Moreover, we will provide spare parts service and maintenance from NSW. A stand....
Brand New 20 Kw Fibre laser cutting machine comes with Precitec cutting Head. 20 Kw Max laser source 4 m X 2m cutting Table. exchange table Water Chiller All in one stabilizer Professional Cypnest software Air compressor....
Discover the FMB Titan Bandsaw Unmatched Strength and Precision Meet the FMB Titan Bandsaw, a powerhouse designed to handle your most demanding cutting tasks with ease and accuracy. Engineered for exceptional performance, the Titan Bandsaw is the ultimate tool for professionals who need reliable, high-quality results every time. Outstanding Features Exceptional Cutting Versatility - The Titan Bandsaw offers precise angle adjustments from 0 to 60 to the right, allowing you to tackle a wide range of cutting angles effortlessly. The manual gravitational operation for version G ensures s....
Features. suits Steelmaster, Amada and all European style pressbrakes hardened and ground finish....
ACCESSORIES Tension Meter, Swivel Base,Bi-metal Blade,Wheel Brush cleaner,Coolant system,,variable speed,Length Stop OPTIONAL ACCESSORIES Spare Blade,Hydraulic Vice,Invertor Speed Control FEATURES One Piece Stand incoorp....
Tecmor model PFT 38 30N Reo Bender Cutter. Specification Capacity Bending 1 Bar 32 mm 2 Bars 22 mm 3 Bars 18 mm Capacity Cutting 1 Bar 28 mm 2 Bars 18 mm 3 Bars 14 mm Size 90 x 98 x 87 cm Weight 430 kg Motor 1.83 kw Feat....
Our Pro-Plas 1.5m x 3.0m machines, with Hypertherm Powermax 65A plasma source, Starfire CNC controller and 12 month subscription to FastCAM professional are one of our most popular models. Machines do move from stock VERY QUICKLY, but there are always new machines either in production, or on the water. These are an industrial quality machine, with a level of finish and build that you just don t find in this price point or with some of the more expensive manufacturers Standard table sizes 1.2 x 2.4m, 1.5 x 3.0m, 2.0 x 4.0m, 2.5 x 6.0m Hypertherm Powermax 45A, 65A, 85A, 105A, 125A avai....
SWIFTCUT Swiftcut PRO 1250WT CNC Plasma Cutting Table 1250 x 1250mm Water Table System Hypertherm Powermax105 SYNC - Cuts up to 22mm Mild Steel Plate CALL NOW AND DO A DEAL ADD THIS ASSET TO YOUR WORKSHOP WE OFFER MACHIN....
Accurl sheet metal machinery offer high level technology machinery within its market segment and is a progressive forward thinking company constantly improving their products and product range. Its because of this Comple....
Used Lockformer Vuclan Waterjet Cutting Machine for Insulation Cutting insulation manually is a slow, costly and inexact procedure. The Lockformer Vulcan 1600 Fiberglass and Insulation Foam Waterjet Cutting System automa....
CNC MACHINERY SALES AUSTRALIA PRESENTS - WS3 Multi-Purpose In-Line Boring Machine ideal for restoring any tapered or worn out hole to its original dimension, standing out for their stability, accuracy, compact size, stur....
Description HVAC Sheetmetal TDC Duct Flanging Machine. Steelmaster Model TDC-T35 1.0, 20 Station, 35mm Flange Can Be Tooled To Suit Optional 20 25 30 or 40mm TDC Profiles - Volt Perfect for all air conditioning ducting a....
ROBOT MOUNTED TOX PRESSOTECHNIK CLINCHING CLINCH TOOL TZ 05.464781 HYDRAULIC PRESS AIR OVER HYDRUALIC INTENSIFIER POWERED BY KRAFT-PAKET EPWX-V3 CEP400 85KN EIN ON 10 OFFSET LIMIT SENSOR 200231 TZ 05.464781 TZ 05N02A320Z....
JAFO Jaracin FWD-32U universal motorised overarm milling machine. 40 ISO spindles, speeds 45-2000rpm vertical amp 31.5-1000rpm horizontal, 313mm x 1230mm swivel table, feeds and rapids. Vertical Huron type with 100mm manual quill feed. Motors 2.2kw vertical, 4.5kw horizontal, 415volt, 3 axis DRO. Has rotary table, arbour supports and arbours. Machine weight approx 2400kg.....
The most-trusted machine retailer in Australia is proud to present to you a used AMADA COMA 567 58 STATION 1989 in superb condition. This machine has been given a comprehensive and thorough refurbishment rebuilt ball scr....